摘 要 通过分析以及使用经验,将工厂主管道蒸汽减压三个方案进行分析比较,从而选用合适的方案,达到*佳的减压稳压效果。
关键词 蒸汽 减压
由于工厂生产工艺的需要,蒸汽是必不可少的工艺介质,需要从电厂输入蒸汽,因电厂到工厂的距离较远存在压力波动较大的情况以及工厂在实际使用的流量波动范围较大,因此在进入工厂的蒸汽主管道压力进行减压稳压。
解决以上问题经常采用以下两个方案,方案一是采用自力式压力调节阀,方案二是采用气动调节阀。
方案一 一台自力式压力调节阀
1 ZZY型自力式压力调节阀 2截止阀 3储气罐 4 安全阀
方案一 采用自力式压力调节阀,因简单方便,维护量小,特别是在现场能适用在无电无气的场合,因此在蒸汽减压的系统中得到了广泛的应用,见以下特点:
1 压力设定点可在压力调节范围内现场调节;
2 阀体部分与执行机构采用模块化设计,可根据现场要求变化更改执行机构或弹簧,实现压力调节范围在一定范围内快速更换;
3 ZZYP自力式压力调节阀一般采用波纹管作为压力平衡元件,阀前、后压力变化不影响阀芯的受力情况,大大加快阀门的响应速度,从而提高阀门的调节精度;
4 ZZYM自力式压力套筒调节阀采用了自平衡型双密封面阀芯作为节流件,介质应清洁无颗粒状杂质,适用于压降较大,阀门口径不大,泄漏量要求不高的场合;
5 ZZYN型自力式双座调节阀采用了自平衡型双密封面双座阀芯作为节流元件,适用于阀门口径较大的场合;
6 膜片式执行机构采用橡胶膜片作为压力检测元件,刚度小,灵敏度高,反应迅速,调节精度高,适用于控制压力≤0.6MPa;
7 活塞式执行机构采用气缸活塞作为压力检测元件,适用于控制压力较高的场合,压力设定值≥ 0.6MPa;
8 波纹管执行机构采用波纹管作为压力检测元件,适用于高温等较恶劣工况的场合。
采用自力式方案中应特别注意以下几个关键点,也是实际应用使用不当经常出现的问题:
序号 |
注意点 |
作用 |
使用不当产生后果问题 |
1 |
阀后应安装储气罐 |
可起到缓冲稳压的作用 |
当流量变化时, 产生压力较大的波动现象。 |
2 |
减压阀后应安装过压保护装置 |
防止阀门被打坏 |
(即安全阀),防止因阀后流量接近为零而导致压力上升,对自力式压力调节阀打坏现象。 |
3 |
安全阀的设定压力不可接近工作压力 |
防止安全阀起跳频繁 |
流量过小时,导致自力式压力调节阀趋向关闭,而产生安全阀起跳频繁。 |
4 |
因尽量减小自力式压力调节阀填料密封处的摩擦力, |
防止因摩擦力过大而产生阀门反应滞后现象。 |
导致阀后安全阀起跳频繁或压力过低现象。 |
方案二 采用一台气动调节阀,特点是调节精度比自力式压力调节阀要高的多,但成本和维护要求较高。
方案二 一台气动调节阀控制
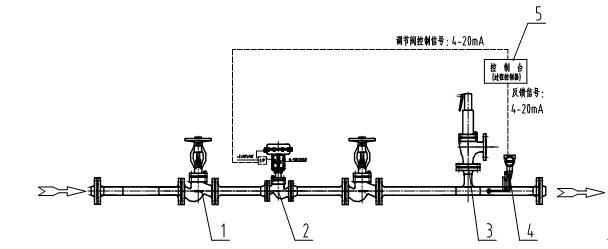
1截止阀 2气动调节阀(附带定位器) 3安全阀 4 压力变送器 5控制台(过程控制器)
压力变送器根据测定的压力反馈4-20ma.DC电流信号,在控制台中与设定值比较,当两者之差达到一定数值后,控制台向气动调节阀发出调节信号。而气动调节阀的执行机构按此信号,使阀杆带动阀芯产生位移,改变通过调节阀的流量,直到测试点压力达到要求.从而达到自动调节压力的目的。
调节阀的结构根据工艺条件基本上为单座、套筒、双座、笼式单座、套筒单座以及低噪音结构。
以上两种方案是工厂的常用的两种方案,但在实际应用当中阀后的流量变化较大,特别是在蒸汽用量很小时,即阀门的开度很小,阀门在小开度情况下不是很稳定,容易出现阀门震荡。解决方案:在此情况下建议用方案三,采用两个气动调节阀并联。
方案三 采用两台气动调节阀并联进行同向分程控制:A阀接收调节仪4~12.5mA时阀门从关闭至全开,B阀接收调节仪11.5~20mA时阀门从关闭至全开,这两台阀门通过两只通向作用的定位器实现。工况在小流量时,B阀处于关闭状态,通过A阀的开度变化来实现。工况在大流量时,A阀全开也满足不了要求时,这时B阀也开启,从而来增加蒸汽的供应量。采用方案三不仅可以满足生产时负荷变化要求,而且提高控制精度和稳定性。