左阀筒零件在半精车后,经过调质处理(HB240~270),材料相应的硬度和机械性能都有所提高(见附图的技术要求)。它的精度要求主要表现在:φ42f8外圆尺寸上,公差较小,表面粗糙度要求高,外圆Ral.6、Ф36密封槽与内螺纹之间有同心度要求。见图1所示。
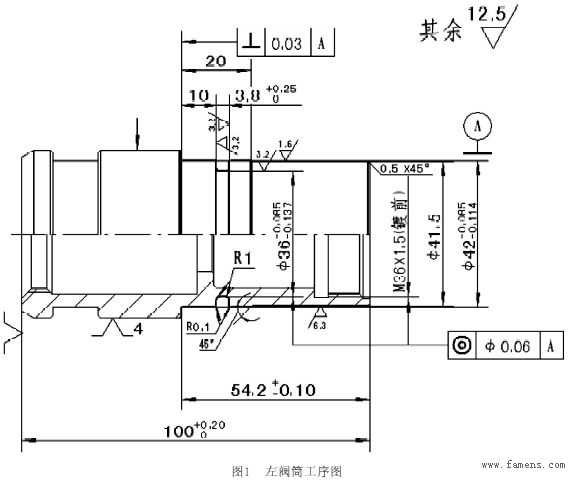
为了保证零件同心度要求,常规的加工方法,也就是在主轴内孔装上限定位,夹住大外圆,在车床上的方刀架上装上四把车刀,割槽刀,外圆车刀,内孔刀,内孔螺纹刀(简称“四把刀”)。由于装刀方向的不同,其中,内孔刀还得锯短,且只有一个螺钉切住它。
常规方法虽然保证了零件的同心度要求,但在工作过程中暴露了诸多问题,这种加工方法也不符合工厂批量生产的原则。具体如下。
1 现象与原因
1.1 外圆尺寸不稳定,表面粗糙度达不到要求
(1)φ42f8的外圆公差只有0.029mm,受转换刀架精度的限制,每做一个需试车一刀、测量一下,增加了停车和测量时间,而且容易出废品。(2)受车内孔螺纹的牵制,只能用中速车外圆,积屑瘤堆积在外圆车刀的前面上,影响外圆的表面粗糙度的要求。
1.2 车内孔螺纹时尺寸不稳定,螺纹表面粗糙
(1)零件半精车后经过热处理,内部组织有所加强。按常规磨60°三角螺纹内孔刀,刀尖角取59°30'时,时常出现螺纹塞规“过端不过、止端过”的现象,而且极易产生“让刀”现象,螺纹表面也不光洁。(2)内螺纹是镀前螺纹,它的中径略大于同类的普通螺纹,在车削过程中,牙根处的金属弹性恢复比牙顶处大,所以它的牙尖角要小于59°30',而且螺纹内孔要车到它的*大值。(3)螺纹表面粗糙是没有合理使用切削液。
2 效率低、费时费工,不符合批量生产
用常规的“四把刀”的加工方法,受到上述原因影响外,还有一个就是无谓的劳动太多:频繁地转换刀架,大、中溜板移进移出,反反复复,很是繁琐与麻烦,既影响了下道工序的加工又影响了自己的效益,更不符合工厂批量生产的原则。
3 改进的方法与措施
3.1 综观上述的分析,首要的是解决同心度的问题,也就是要改进装夹方法
(1)选用软卡爪装夹。选用铸铁做成的软卡爪,它具有耐磨、吸震的功效。特点是工件虽经多次装夹,仍能保持一定的三点相互精度(一般在0.05mm),可减少大量的校正时间,而且不易夹伤已加工表面。
(2)卡爪两边各以15°的角度铣掉,留有4~6mm宽的圆弧面,以利于夹紧零件。见(图2)
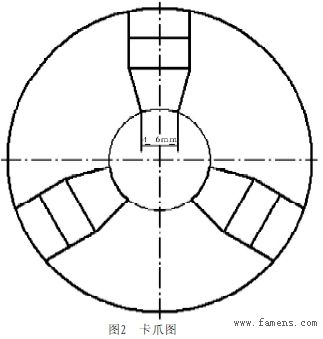
(3)在卡爪中间开出一条宽4×4mm的槽,用于放置宽3.5mm厚为3.5mm直径大于夹紧零件直径的定位圆环。这圆环起着车削软爪时消除间隙的作用。圆环放置应跟零件的装夹方向一致,并作上标记(见图3)。
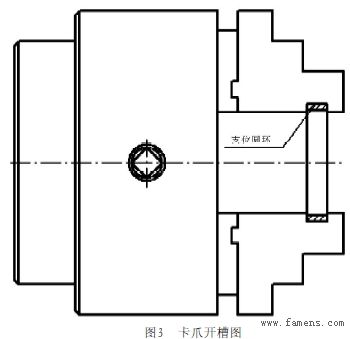
(4)车削软爪时,由于是断续切削,易低速、小走刀,但*后一刀要从里往外车。车削卡爪的直径需跟被装夹零件的直径基本相同(允差±0.05mm)。
3.2 统一装夹基准
每次装卸零件时,都要固定使用做了标记的同一个板手孔。零件夹紧之后、在车之前,用能做标记的物体顺着有标记的卡爪边给零件划一条直线作为零件的标记,下次装夹以此为基准。夹紧力要均匀一致。改变板手孔位置和夹紧力的大小都会改变卡盘的移动量,而影响装夹后的定位精度。经试车和反复的测试,认准板手孔与零件划线的位置,同心度始终保持在0.02mm以下。装夹基准的统一,较好地解决了同心度,减少了定位误差,提高了精度,为下一步批量生产提供了有力保证。
3.3 简化了刀具,提高外圆的表面精度
(1)有了软卡爪的保证,“四把刀”可弃之不用,取而代之为横向装一把宽些的外圆槽刀,既可车外圆又可内孔,摆脱了反复转换刀架的束缚与车内螺纹的牵制,车削速度得到提高。(2)车刀采用0°的修光刃(约为走刀量1.2~1.5倍),放大走刀量,并经常用油石研磨车刀的前面与后面、副后面,提高刀具表面粗糙度,让积屑瘤无立“足”之地,基本上达到了外圆表面粗糙度Ra1.6的要求。
3.4 改进刀具,合理选用切削液,提高螺纹表面精度
软卡爪装夹保证了同心度,槽、内螺纹可单独也可合并在一起加工。(1)由于内螺纹M36×1.5﹣6H为镀前螺纹,按常规刀尖角为59°30'则是过大了,应该把刀尖角减为57°~58°,才能取得*好的效果。(2)切削液可选用(80%~90%菜油﹢10%~20%煤油),因为它保证切屑层均匀,切削深度小时不致于造成“让刀”,可以提高螺纹精度和表面质量,并延长刀具的寿命。
4 结语
采用软卡爪装夹,常规加工方法产生的诸多问题,基本上都迎刃而解了。从表面上看,看似多了一道装夹车内螺纹与割槽的工序,但它符合工厂批量生产和流水线作业的原则,符合生产类型和工序的集中与分散的原则,而且生产效率得到了较大提高,产品的质量也得到了保证。随着科学技术的进步,数控机床在企业已逐步普及。我今天所论述的问题在数控机床上加工已不是问题了,但这种思维的方式与改进加工的方法是永不会淘汰的。所以合理地改进加工方法,采用合理的措施,它照样能使普通机床闪出耀眼的光芒!
参考文献
[1]上海**毛麻纺织机械厂.车工实践[M].上海科学技术出版社,1974.
[2]金福长.车刀绝技[M].中国工人出版社,1992.
[3]张维记编.车工实用手册[M].浙江科学技术出版社,1993.
[4]机械工业部.车工工艺学[M].机械工业出版社,1980.
[5]机械工业部.车工[M].机械工业出版社,1979.