1 引言
空间用阀门一般具有密封性好、重量轻、操作灵活省力等特点,在设计时既要考虑活门所需的*小密封力,又要考虑*小开启拉力。从理论上讲,密封力越大,密封性能越好,而阀门所需的开启力也就越大,这给阀门的设计带来一定的难度。
在满足*小开启力设计的约束条件下,保证阀门密封性能,确保其可靠性和安全性是设计的关键。影响密封的因素有很多[1],主要因素包括:密封面的表面状况、密封面材料、密封面宽度、密封比压等。其中密封面的加工精度和表面粗糙度越高[2],则密封面的间隙越小,从而有利于密封,尤其是由于*小开启力的限制,密封比压较小,密封面的加工精度和表面粗糙度的影响更加显著。
通过分析计算及验证试验[3~5],一方面,对产生密封力的弹性元件进行优化设计,合理筛选、控制相关工艺参数,严格性能参数筛选,保证所需的密封力的同时,又能满足*小开启力的要求;另一方面,对阀体的设计加工提出更高的要求,严格保证加工精度,尤其是阀口密封面的成形和表面质量。采取以上措施,既保证了阀门具有良好的密封性,又保证了阀门操作的*小开启拉力。
由于该阀体结构的特点,不能采用常规的方法检测密封座的加工精度和表面质量,本文提出了采用微观显微的检测方式,解决了该检测问题,并经过试验验证,得到了满意的结果。此方法的实现,能够更好地保证阀门密封的可靠性、安全性。
2 阀体结构特点及加工难点
2.1 阀体结构特点
为了保证阀门的可靠性和安全性,阀体结构设计成大小两个活门座,形成双密封结构。在一道密封失效的情况下,还有一道密封作保证。具体阀体结构和尺寸如图1、图2所示。
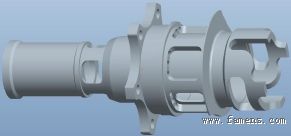
图1 阀体结构实体模型图
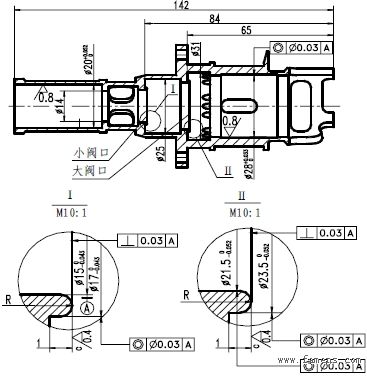
图2 阀体结构设计示意图
阀体总长142mm,小阀口直径Φ15mm,阀口半径R0.5mm,要求阀口表面粗糙度为Ra0.4μm,形位公差为:垂直度0.03mm,同轴度0.03mm;大阀口直径Φ21.5mm,阀口半径R0.5mm,要求表面粗糙度为Ra0.4μm,形位公差为:垂直度0.03mm,同轴度Φ0.03mm;从阀体端面到小阀口底面的长度为84mm,从阀体端面到大阀口底面的长度为65mm,阀体材料为2A12硬铝合金,材料状态为T4。
2.2 加工难点
由于阀体端面到阀口的距离深度较深,且两道阀口的垂直度、同轴度要求高,在切削加工时,操作者无法观察和测量阀口的表面状态和轮廓尺寸,这给阀口的加工和检测造成较大的难度。目前采用的方法为:每批产品投产时,在进行正式加工前,先行投产一件工艺件。在工艺件上,利用专门制作的阀口成形样板刀,进行阀口的摸底加工和工艺参数的确定。然后,将固化后的加工工艺移植到正式阀体阀口的加工上,使大、小两个阀口一次加工成形,靠刀具来保证阀口的成形、表面质量和加工精度。
3 阀口成形及表面质量检测
阀口成形状态和表面质量的好坏直接影响阀门的密封性。由于阀体结构特点所限,使阀口加工时进刀位置较深。在阀体加工过程中或在加工完成后,无法采用常规的检测手段,直接对阀口的相关尺寸及表面质量进行测量。普通量具无法进入阀体内部检测,而内窥镜由于放大倍数不够,观测不到阀口表面的加工纹络、加工缺陷,不能对阀口加工精度和表面粗糙度准确判定。目前的做法是,利用在工艺件上确定的工艺参数,同时固定设备,固定人员,利用成形样板刀,同批加工数个阀体零件的阀口,待阀体零件全部加工完成后,从中随机抽取一件进行剖切,来检验和计量阀口的成形尺寸和表面质量。通过上述加工和检测方法,阀体阀口的加工精度及表面质量总体上得到了控制,也取得了较好的效果。但从阀门组装后氦质谱检漏的结果来看,仍存在加工不一致性的问题。经分析认为,理论上,同一批工件,若采用同样的工艺参数,同一台加工设备,同一个操作者,同样的刀具,阀口的成形状态是不会改变的,加工质量可以保证。但实际上,由于整个加工过程毕竟靠人工操作,难免有些因素考虑不周,加上加工位置不好,操作上存在一些差异性也是有可能的。这种细微的差异,由于阀口位置深度所限,一般用肉眼很难发现,借助45倍体视显微镜,就能明显地观察到阀口的微观形貌及缺陷情况,如图3、图4所示。从图3可看出密封座表面的加工纹络,从图4可看出密封座表面加工后形成的凹坑缺陷。利用显微检测方法,可发现局部微小缺陷,对阀口的表面质量作出准确的判断。
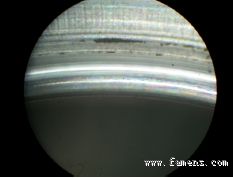
图3 典型的阀口微观形貌照片(45倍局部)
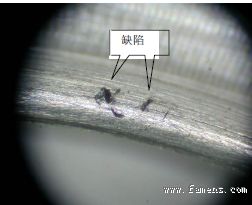
图4 典型的阀口缺陷照片(45倍局部)
4 阀口微观检查及分析
在45倍体视显微镜下,对同批加工的3件阀体的大阀口用45倍的体式显微镜进行检查。从观察到的微观图像来看,每个阀体(1#、2#、3#)的微观形貌各不相同,如图5、图6、图7所示。1#阀体阀口表面质量好,基本看不到切削刀痕纹路,方向一致,平整均匀;2#阀体阀口能看到刀痕纹路,但有轻微划痕缺陷;3#阀体阀口,能清楚看到刀痕纹路。这种阀口表面状态加工的不一致性,势必对阀门的密封性造成影响。
图5 1#阀口形貌照片(45倍局部)
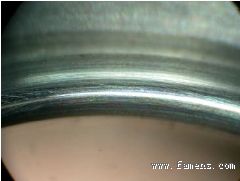
图6 2#阀口形貌照片(45倍局部)
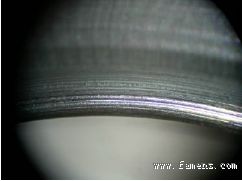
图7 3#阀口形貌照片(45倍局部)
5 试验验证结果
图8 阀体检漏结果
用上述三个阀体与其它零、部件组装形成阀门后,分别对三个阀体在同一状态下进行氦质谱真空检漏,检漏结果见图8,具体数值为:1#阀体*好,漏率为5.86×10-9Pa·m3/s;2#阀体*差,漏率为6.12×10-8Pa·m3/s;3#阀体中等,漏率为1.35×10-8Pa·m3/s。比较三个阀门的漏率结果可以看出,1#阀体的漏率值比2#和3#小一个数量级,2#、3#阀体没有数量级上的差别,只是在同一量级范围内有不同。漏率检测结果与上述显微镜观察到的各个不同阀口微观形貌状态吻合。试验结果表明:通过显微微观形貌的观察,可以检查阀口表面质量的差异,能够反映出阀口加工的不一致性和局部微小缺陷,进而表现出对阀门密封性造成的影响。
6 结束语
a.由于阀体结构的复杂性,设计上造成阀口位置较深不易检测的缺陷,可通过固化工艺参数,进行一定数量阀体的加工。完成加工后,从同批次阀体中,采用抽样剖切的方法检验阀口的外形尺寸及表面质量是一种实用的检测方法。但该方法仍存在不足,由于各阀体加工过程中还存在一定的不一致性,致使阀口一些微小缺陷利用常规检验手段难以发现,进而影响到产品质量;
b.利用显微检测方法,通过显微图像观察阀口的微观形貌和发现局部微小缺陷,对阀口表面质量作出准确的判断,起到了良好的效果。同时是对剖切检验方法的一种补充;
c.在对阀体剖切检测阀口表面质量的同时,再结合显微检测不外乎是一种好的检测方法。这样可使每个阀体阀口的表面质量都得到检测,通过对每个阀体微观形貌的观察和细部微小缺陷的显现,准确判断阀体阀口的表面质量,进而确保产品的密封质量和可靠性。
参考文献
1 高扬.浮动球阀的密封比压分析.兰州:兰州理工大学,2006:23~25
2 蔡艳汪,哲能.表面粗糙度参数对密封性能的影响分析.机械工业标准化与质量,2009(6):40
3 王波,矫桂琼,赖东方,等.真空结构橡胶密封圈的泄漏率分析.西北工业大学学报,2010,28(1):129~132
4 任晓.三维粗糙表面的表征及其气体密封性能研究.大连:大连理工大学,2009:1
5 殷参,王延荣,李荣贵.橡胶O型圈静密封数值模拟.机械设计,2006(8):324~325