中国石油天然气股份有限公司独山子石化分公司220kt/a乙烯装置裂解气压缩机组驱动透平(10-DST-201)为日本三菱公司整体制造,自2002年9月投用以来,机组速度控制系统运行良好。但自2004年10月以来,10-DST-201汽轮机进汽调节阀的反馈系统开始出现振动,而且振动越来越剧烈。由于进汽调节阀的反馈系统直接影响压缩机的转速控制,因此对压缩机的长周期稳定运行是一个重大隐患。针对上述情况成立攻关小组,通过采取一系列有效措施降低调速器反馈杆系统振动,保证机组长周期运行。
1 调速系统反馈杆振动状况及原因分析
1.1 机组速度控制系统工作原理
安装在驱动透平转速齿轮处的2个速度传感器,在测得转速信号后将信号送入WOODWARD电子调速器,电子调速器中的速度控制模块经过运算后,通过电子调速器中的比例限制器,将进汽调节阀和抽汽调节阀的控制信号(20~160mA电流信号)分别送至透平进汽调节阀和抽汽调节阀在现场的致动器中,将电流信号转换成成比例的活塞位移量和成比例的致动器输出轴转角量,*后通过现场的液压执行机构(油动缸和导向滑阀)和反馈机构的联合作用,实现对透平进汽调节阀和抽汽调节阀开度大小的控制,*终通过改变进入透平做功的蒸汽量来控制机组的转速。
图1为汽轮机进汽调节阀反馈系统现场示意。
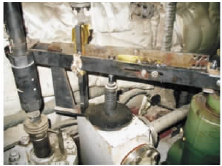
图1 汽轮机进汽调节阀反馈系统现场示意
1.2 改造前反馈系统运行状况分析
2006年10月12日联系石化公司设备研究所专业人员对进汽调节阀反馈系统振动进行了测绘,相关数据见表1。
表1 进汽调节阀反馈系统振动数据 mm/s
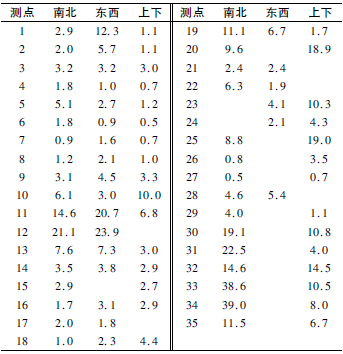
通过表1可看出:进汽调节阀反馈系统振动(正常值≤15mm/s)已影响到机组安全运行。
图2为汽轮机进汽调节阀反馈系统测点示意。
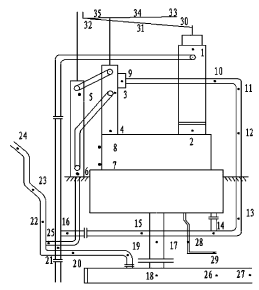
图2 汽轮机进汽调节阀反馈系统测点示意
1.3 振动原因分析
根据采集到的振动数据并会同相关人员分析认为振动产生的主要原因是汽轮机转子产生的一倍频振动传递到调速器连杆,引起调速器连杆的共振,导致整个汽轮机进汽调节阀反馈系统振动加大。
2 对进汽调节阀反馈系统进行加固以减小振动
2006年5月9日技术人员制定出具体方案,在致动器输出轴、控制器挡板、反馈杆的关节轴承和反馈板的定位叉处进行了加固,减小了进汽调节阀反馈系统的振动与磨损。同时更换了反馈系统夹板销钉铜套。
图3为致动器输出轴部位示意,致动器夹板用自制的钢板夹住,来降低致动器处振动。
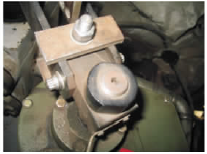
图3 调速系统致动器输出轴部位示意
图4为控制器挡板调节辊轮处,制作安装铜帽,保持挡板不致磨损。
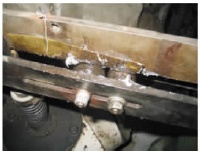
图4 控制器挡板示意
图5为反馈杆的下部关节轴承,注意检查连结轴两侧螺帽是否紧固,转动关节轴承连杆,查看关节轴承的连接处是否紧密、灵活、无脱开,铁丝是否紧固。
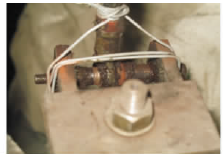
图5 反馈杆的关节轴承连接示意
图6为反馈板的定位叉处,反馈杆夹板与定位叉接触部位加两片铜皮,防止定位叉振动磨损。
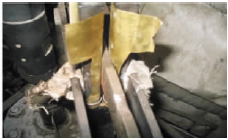
图6 反馈板的定位叉示意
加固之后反馈杆震动明显减小,通过约30天的观测,反馈杆的磨损增长不明显。实践表明反馈杆的加固方案行之有效。
3 进汽调节阀反馈系统组件改造及更换
3.1 进汽调节阀反馈系统组件改造
技术人员对现有调速系统经多次现场会诊并查阅大量机组资料,认为现有调速器反馈系统组件强度不够,长时间振动后导致各部件磨损严重。因此通过联系厂家技术人员要求针对高频振动和磨损情况对反馈系统组件进行改造,在不影响现场实际安装的情况下,将反馈系统组件的尺寸加大,加厚,以解决反馈系统的高频振动和磨损问题。
表2 改造前后反馈系统组件尺寸对比 mm
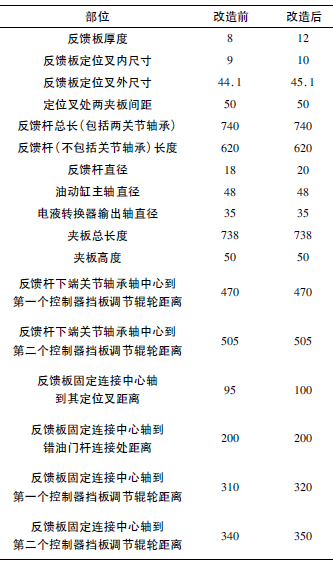
3.2 机组检修期间对进汽调节阀反馈系统组件进行更换
2007年8月25日利用停机检修时对调速系统反馈杆组件及致动器进行了更换,更换的新组件较以前的材质强度加大,各振动部件均加宽加厚,并进行热质处理,保证其抗振性能。
4 改造后效果
从2007年9月1日压缩机开机运行至9月15日机组提至*大负荷,经半个月观察,进汽调节阀反馈系统组件振动比检修前有根本性的好转。
2007年9月16日联系设备研究所对进汽调节阀反馈系统振动进行了专业测绘,相关数据见表3。
表3 进汽调节阀反馈系统振动数据 mm/s
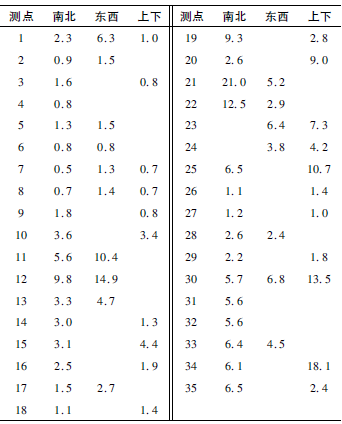
通过与表1比较可以看出:汽轮机进汽调节阀反馈系统振动有了根本性变化,振动明显减小,说明改造收到了很好的效果,从而保证了机组的长周期运行。
5 结语
从汽轮机目前运行情况来看,进汽调节阀反馈系统还是存在轻微的振动,已对其做了加固处理。另外每周会同钳工人员对其进行检查及润滑,保证进汽调节阀反馈系统工作正常,保证机组安稳长运行。